How a Martello Employee Provides Face Shields in a Time of Crisis
#MartelloLife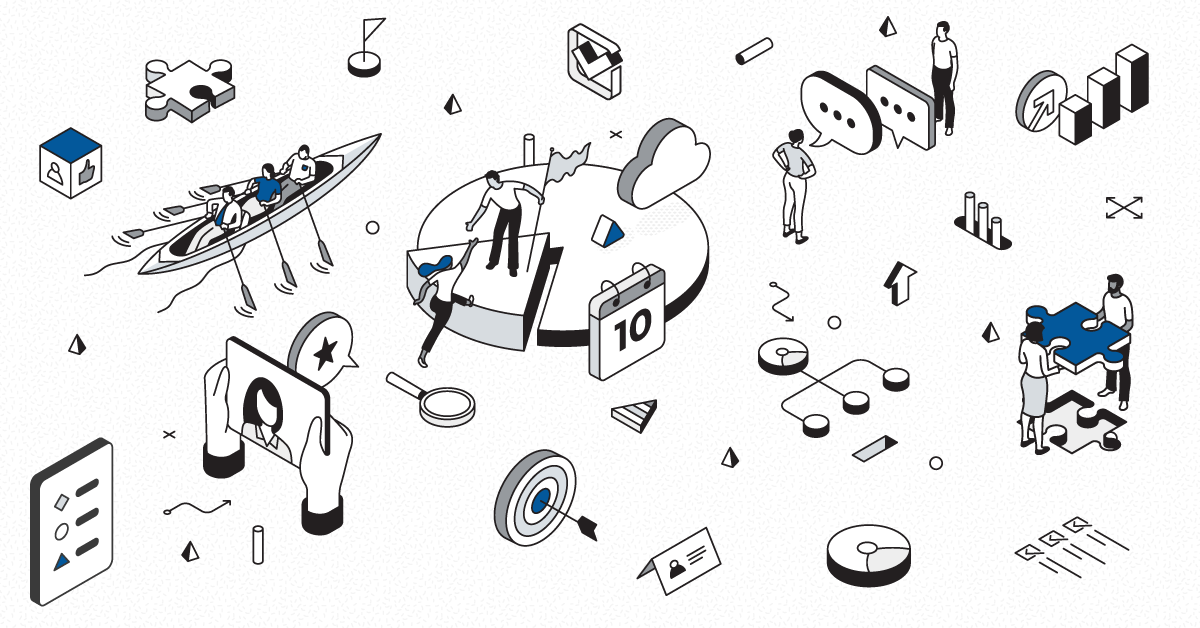
Protecting our front-line workers as they battle COVID-19 has become a focal point for many people in the community. Using the resources and skills at our disposal can make the difference between life and death for many people.
Front-line workers rely on many items to keep them safe when interacting with patients. This includes masks, gloves and face shields.
Bill Kuker, of Martello, is a founding member of The MINT Rutland’s Makerspace. The MINT is a shared workshop and classroom for anyone in the community who is interested in making things. Often hobbyists, DIY enthusiasts, educators, students and entrepreneurs don’t have available space or can’t afford to own a workshop filled with the tools they need to turn their ideas into reality. With the ability to make almost anything, The MINT has turned their attention to making face shields to helping front-line workers protect themselves when social distancing isn’t an option.
“So the hospital said if we had face shields — they’re … the plastic things you’ll see emergency workers wearing over their mask — it prevents a lot of the aerosolized stuff from being breathed in anyway, and they are running short on those,” Peg Bolgioni, hospital spokeswoman said. “The specific thing about that plastic that’s great is it’s already used in the medical field because it can be sterilized, and it’s thin enough that our design requires it to be flexible to get bent, and so that’s what’s going to work.”
So far, the team of makers have made over 400 face shields for the local hospital, with a goal of producing 10,000.
Working with staff from the Rutland Regional Medical Center, a team of volunteers from The MINT has developed a face shield that is laser cut from a single piece of 0.020 PET plastic in less than a minute, ships flat and folds to use.
See how they’re made:
The biggest challenge this initiative faces is getting the supply of plastic to print the shields. Funding is also needed to help to purchase the materials in order to create the shields. Once they have the supplies, they can produce 1,000 face shields in an eight-hour shift. These cut shields store flat for easy transport and only take seconds to assemble for use.
“As far as actual money goes, some parts of this project are just sending a guy in a van with a fistful of dollars to places that have some of the plastic in supply,” Martello’s Bill Kuker said. “We are all personally fronting the cash, so any donation is helpful.”
Each shield costs between $1-3 to make, depending on the materials the team is able to secure. The face shield design is open source and freely available.
Martello is happy to support this initiative through a financial donation using our Employee-Directed Gift Program and it is the second donation that has been made in recent weeks to support COVID-19 relief.
After the launch in 2016 of Martello’s Employee-Directed Gift Program, employees were empowered to make a deeper connection and financial contribution to the community organizations that matter the most to them. Through this program, Martello has been able to contribute to local sports teams, getting kids out on bicycles, helping students travel and provide aid to those who need it, providing education support to indigenous students, supporting a hack-a-thon for health, giving support to a Cochlear Implant group, and serving underserved communities.